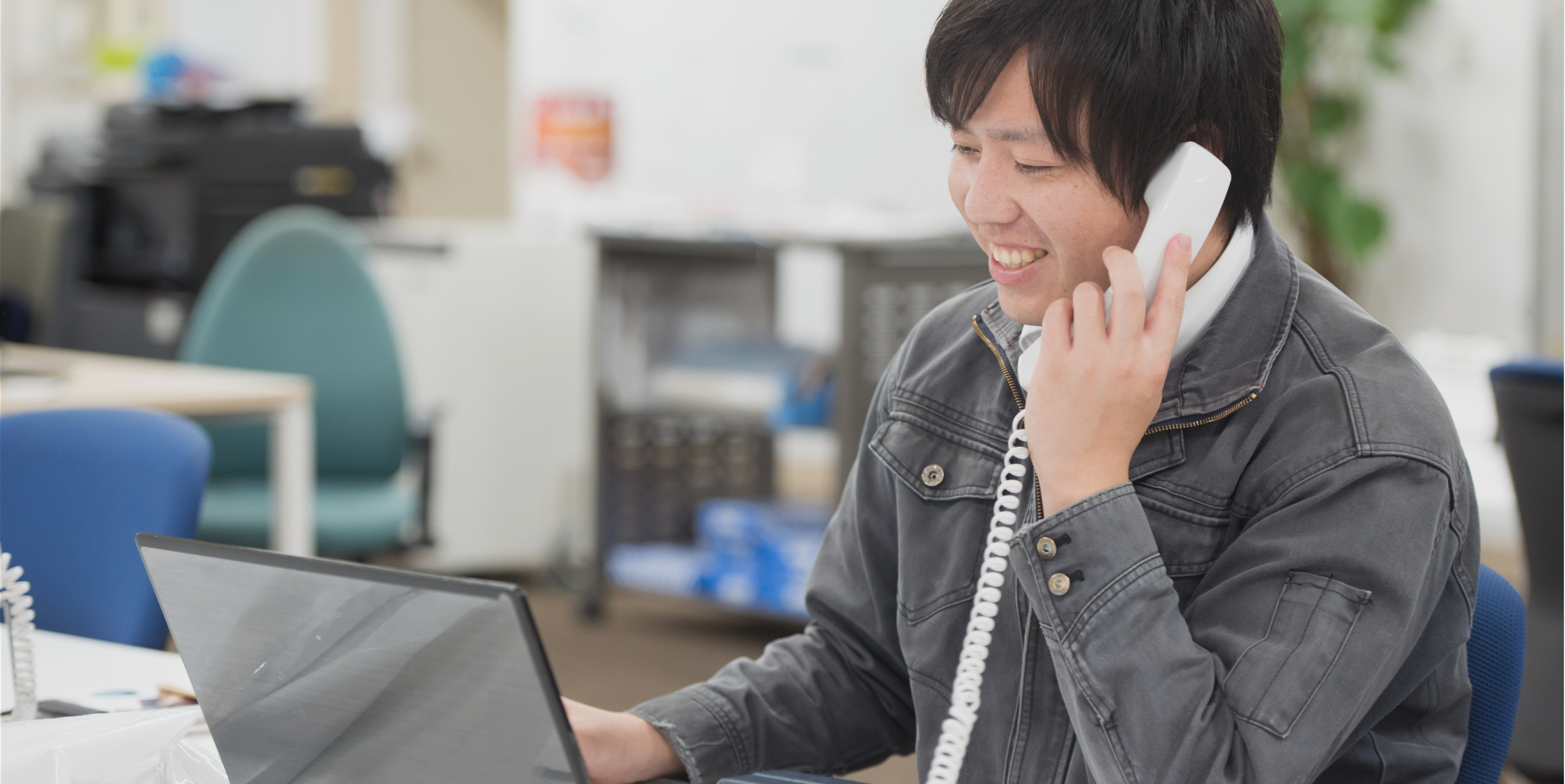
なぜサカエのFA・自動化が、
多くの加工工場・組立工場に
選ばれるのか
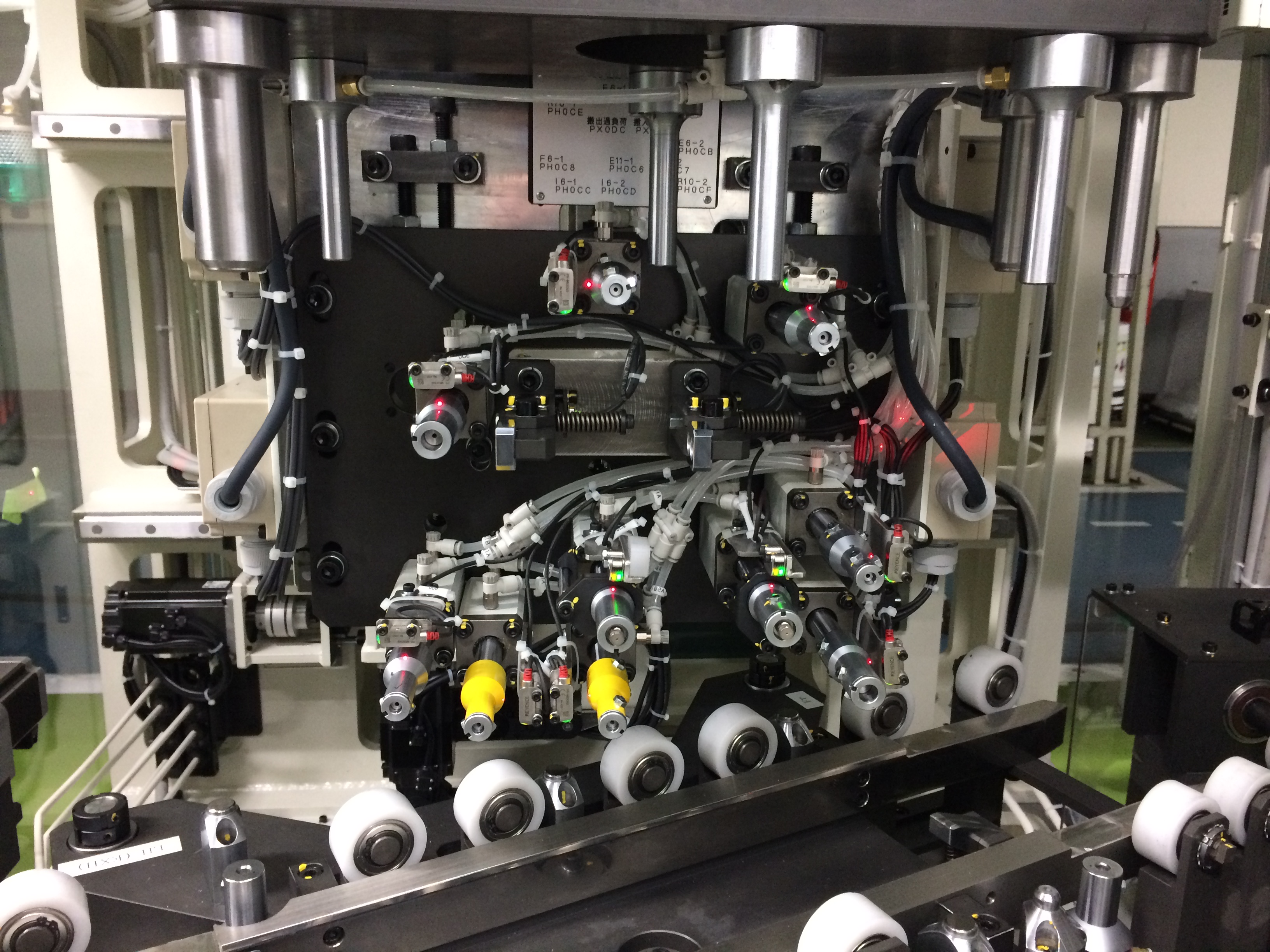
自動車工場の組立工程を自動化
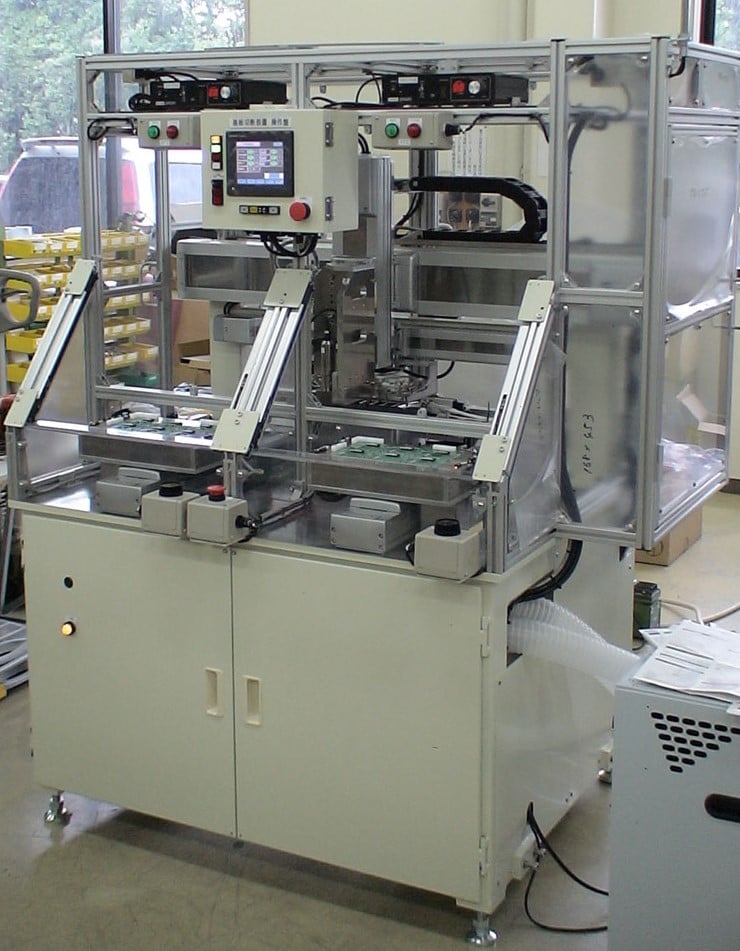
家庭用エアコン工場の加工工程を自動化
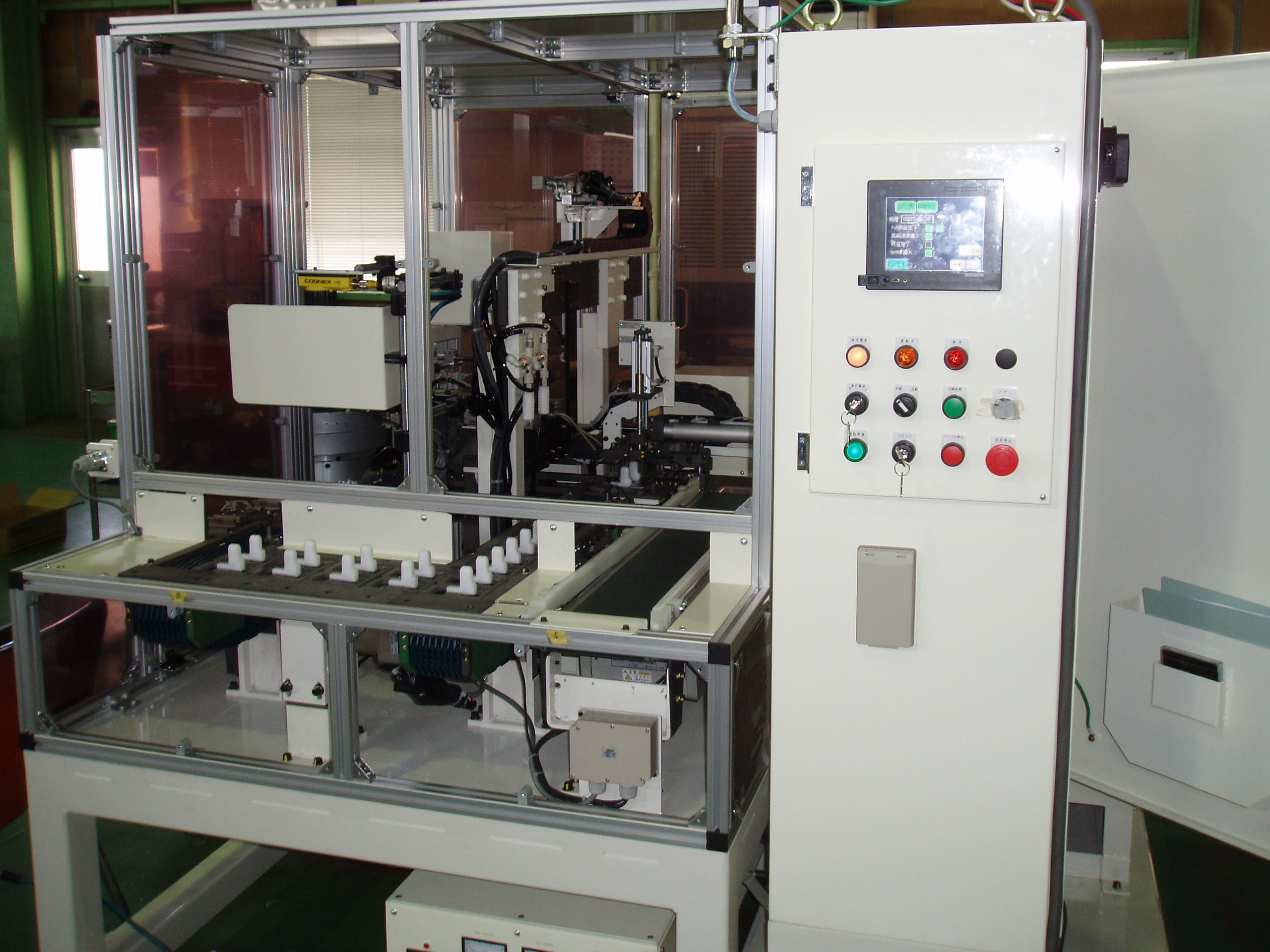
自動車部品工場の加工工程を自動化
%20(1).jpg)
自動車部品工場の測定工程を自動化
%20(1).jpg)
自動車工場の洗浄工程を自動化
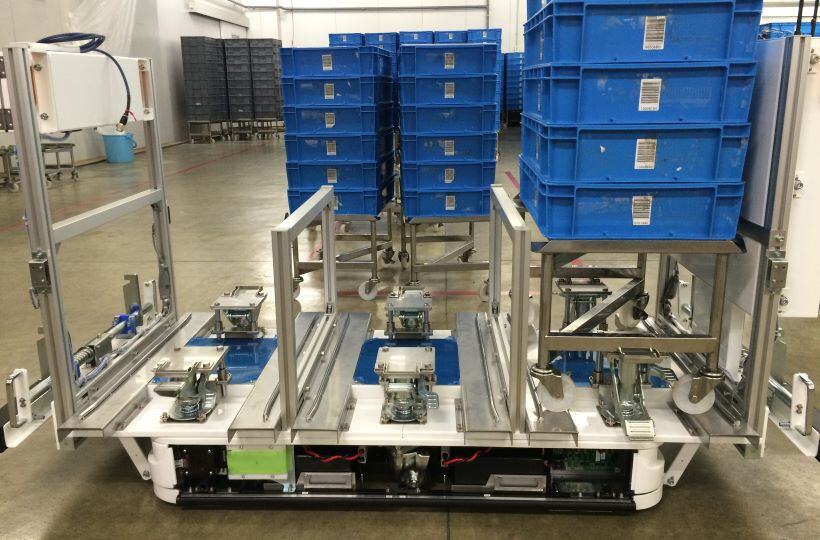
工場の出荷倉庫の搬送工程を自動化
株式会社サカエによる自動化導入!4つの特徴
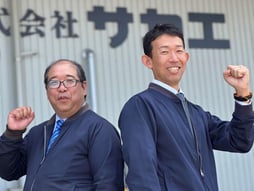
1
150社以上・1500台以上の豊富なFA・自動化実績!
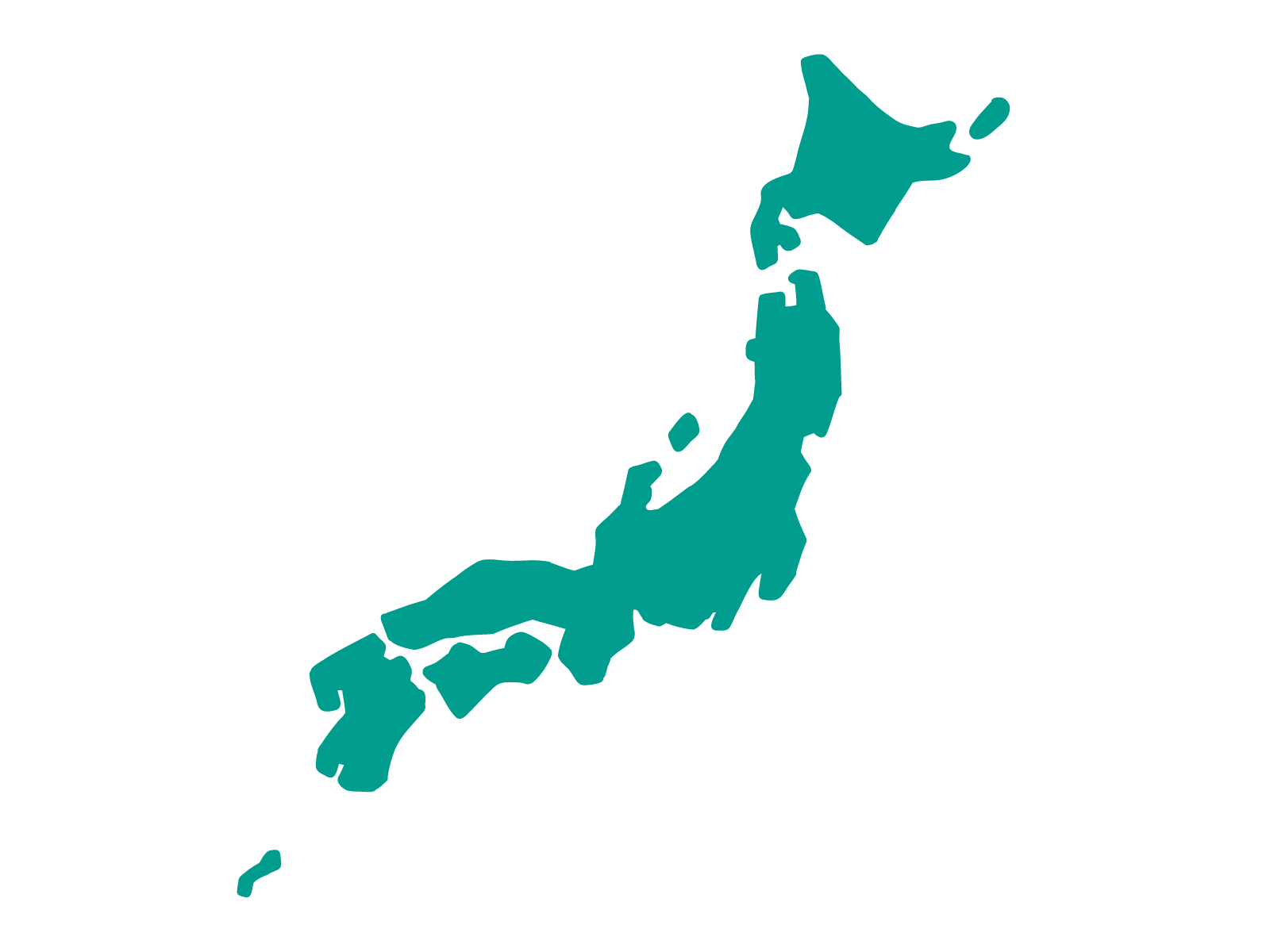
2
モノづくりエリア東海4県の実績を元にエリア拡大中!
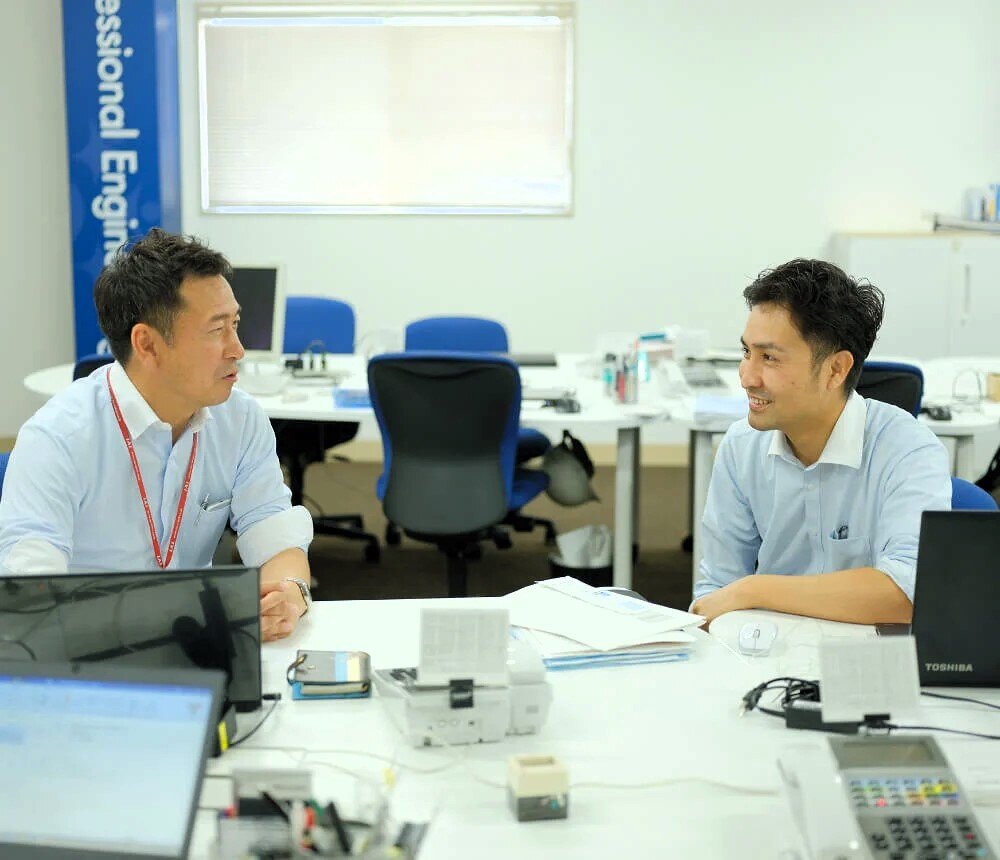
3
専門家集団として構想から納入までワンストップで対応可能!
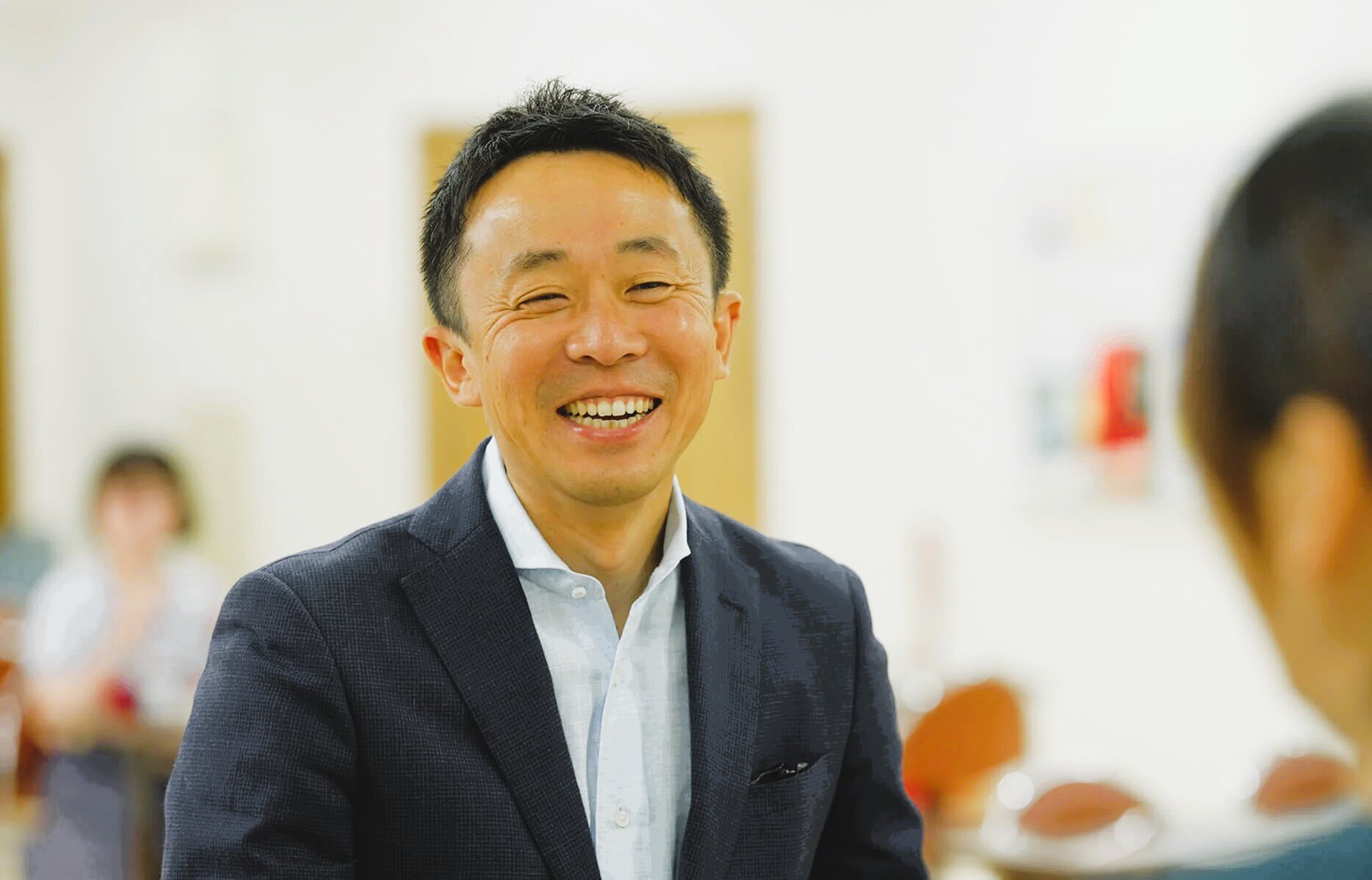
4
創業70年以上。安定・安心の体制でお客様に寄り添います!
現場の課題!当てはまるなら、要・自動化!
ひとつでも、あなたの会社の現場に当てはまるなら
もっと自動化の検討を
もっと自動化の検討を
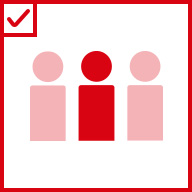
人手不足に歯止めを!
製造ラインを小さなことからでも自動化すれば「作業者の減」に。
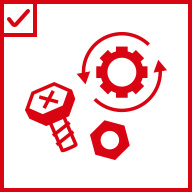
品質を安定させたい!
作業者の熟練度・働き方の変化・後継者問題などを自動化で解消。
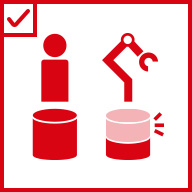
原材料費高騰の対応!?
自動化の利点はミス防止・不良削減。結果、原材料/光熱費の削減に。
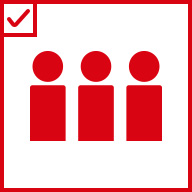
採用・定着を何とかしたい
「きつい」「汚い」「危険」の3K工程は「自動化する」が今風です。
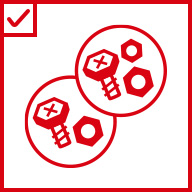
生産数の「脱バラつき」を
手作業では生産数にバラつきが…。自動化は生産数を安定させます。
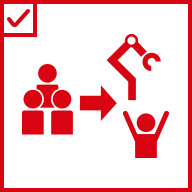
人件費を本気で抑えたい
人件費削減以上に、高付加価値な仕事への人員配置にも自動化は◎。
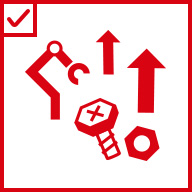
生産数をアップしたい!
24時間働くのが設備の強み。作業スピードと生産数を各段にUP!
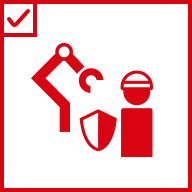
キケンな作業をなくしたい
高所の作業・重量物の搬送などは自動化で! 時代は脱・危険作業。
お電話 or オンラインで、まずはお話ししましょう!
自動化したけど
効率が上がらない!
効率が上がらない!
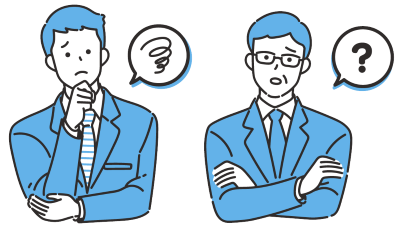
機械を入れたけど
動かせてない!
動かせてない!
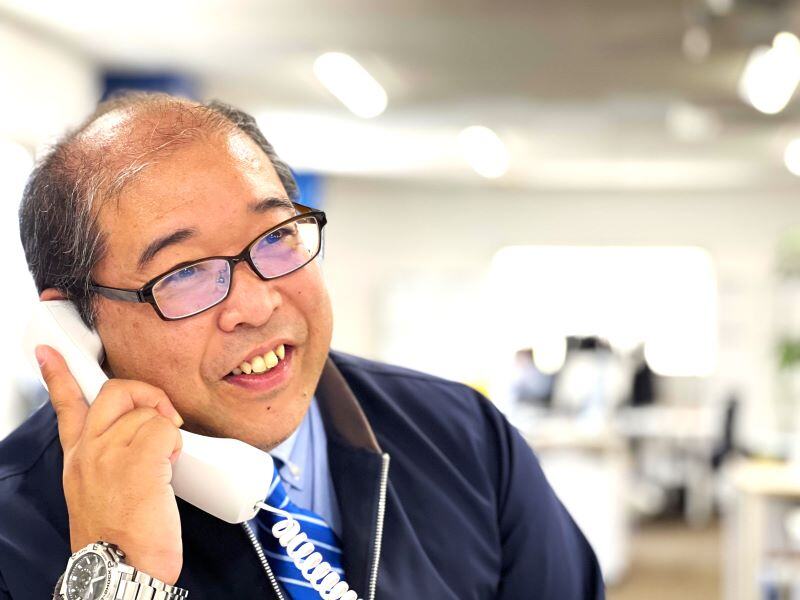
そんな現場の相談も受け付けています
電話 or オンラインで
お気軽にどうぞ!
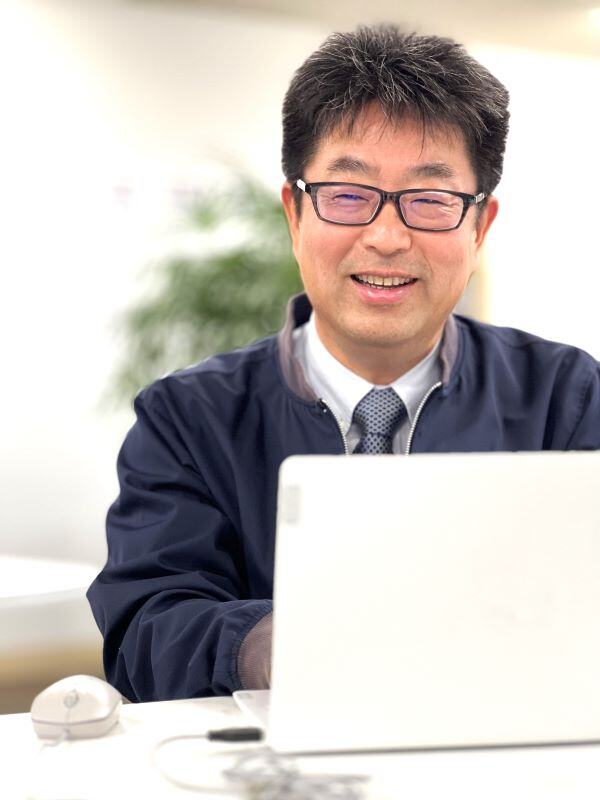